Luther Boardman
- Born: 26 Dec 1812, Stepney CT
- Marriage (1): Lydia Ann Frary on 18 Oct 1838 in Meriden CT
- Died: 29 Mar 1887, East Haddam CT
General notes:
Pewtersmith
Events in his life were:
- He worked in 1835 as a pewtersmith in South Reading MA having purchased the business of Burrage Yale. 31
- He worked in 1837 as a pewtersmith in Meriden CT 31
- He worked in 1838-1842 as a pewtersmith in Chester CT 31
- He worked in 1842-1887 as a pewtersmith and silverplater in East Haddam CT with his brother Norman as clerk. 31
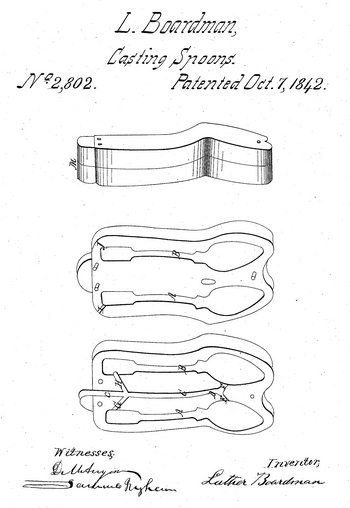
- Patent: 2,802, on 7 Oct 1842. LUTHER BOARDMAN, OF EAST HADDAM, CONNECTICUT.
IMPROVEMENT IN THE MANNER OF FORMING MOLDS FOR CASTING SPOONS, &c.
Specification forming part of Letters Patent No. 2,802, dated October 7, 1842.
To all whom it may concern:
Be it known that I, LUTHER BOARDMAN, of East Haddam, in the county of Middlesex and State of Connecticut, have invented a new and useful Manner of Forming Metallic Molds for the Casting of Spoons and other Articles; and I do hereby declare that the following is a full and exact description thereof.
In the accompanying drawing, K represents one side of a metallic spoon-mold, which is formed in the ordinary manner, and L is the reverse half. M shows the two parts as they appear when united, so as to be ready to receive the melted metal.
The improvement made by me consists in the manner in which I form, the gate or channel by which the metal is to enter the mold. In casting spoons I usually cast two in the same mold, as this is more economical than casting them singly, although the latter may be done upon the same principle as that which I adopt in forming them in pairs.
A B represent the cavities formed in the molds for the reception of the metal. C C is a gate or channel through which the metal is to enter, and which is continued down to the point I), where it divides into two channels, one leading to each spoon in a descending oblique direction, as reprented at E and F in the drawing. Toward the upper end of the main gate there are two other gates or sprues leading from the main gate C C, and connecting it with the upper portion of the cavity for the articles to be cast. These gates or sprues are made to incline upward, as shown at G H. From the upper end of each spoon or other article there is usually a small air-channel leading upward, as shown at I J. This completes the formation of the mold.
The improvement in this mold consists, in the particular manner in which the main gate C C and the lateral gates or sprues E F and G H are arranged and combined with each other and with the cavities in which the spoons or other articles are to be formed, said form and arrangement of the gates being especially adapted to the casting of spoons and similar articles in metallic molds. In the ordinary manner of casting spoons in such molds the metal is poured, in by a gate leading directly into the upper portion of the cavity, and the result is that the scoria, which is always forming in the metal, accumulates in the upper end or handle, and renders the article more or less porous in that part—a defect which is rendered evident in the process of finishing the article with a buff. By my arrangement the metal enters at a certain distance above the lower end of the article to be cast, as at E F, where it corresponds with the broadest part of the bowl of a spoon, and it continues to rise in the cavity or cavities until it arrives at a level with, the upper lateral gates, as at G H, when it flows in through those channels, and when thus introduced the upper end of the article will be found to be perfectly free from all visible porosity.
I am fully aware that articles have frequently been cast in sand by causing the gate to descend to the lower part of the cavity made in the flask by the pattern, and allowing the metal to flow regularly upward, this having been done to prevent injury to the face of the mold in the casting of fine work by the descent of the molten metal in a continued current along it; but in metal molds the object to be attained and the means of attaining it are different from those just described in casting in sand. Metallic molds, which are good conductors of heat, require to be kept at a given temperature to admit of the setting and removal of the cast article without waste of time, while it is important that this setting shall not be so sudden as to cause it to take place before the article is perfectly formed. Now, in an -article of the length of a spoon it will be found that if the metal is allowed to descend along a gate to its lower end and then to ascend to the upper end by the pressure of that contained in the gate the spoon cannot be cast without keeping the mold at a temperature which would defeat the object; but by means of the two lateral gates or sprues to each spoon, arranged in the manner or substantially in the manner herein described and represented, the desired end will be attained.
Having thus fully described the manner in which I construct my metallic molds for casting spoons and other articles of a similar character, what I claim therein as new, and desire to secure by Letters Patent, is—
The forming of such molds with a main descending gate leading down nearly to the lower end of the spoon or other article to be cast, where it is to communicate with the proper cavity by means of a lateral descending gate or sprue, in combination with the sprue above this and toward the upper end of the cavity for receiving the metal, having an ascending direction, the whole being formed in the manner and for the purpose herein fully set forth; and I will here remark that, although I have spoken of a single lateral ascending gate of sprue leading to each, cavity, there may be two or more such lateral ascending gates without producing any injury, although I do not think them necessary or desirable.
Luther Boardman
Witnesses:
Thos. P. Jones
Edwin L. Brundage
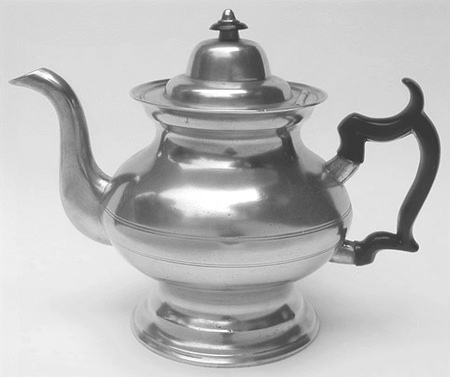
- Example: Teapot, circa 1845, in Private Collection. H: 7 1/4" (including finial)
- He appeared on the census in 1850 in East Haddam CT. Listed as a spoon manufacturer.
- He appeared on the census in 1860 in East Haddam CT. Listed as a manufacturer.
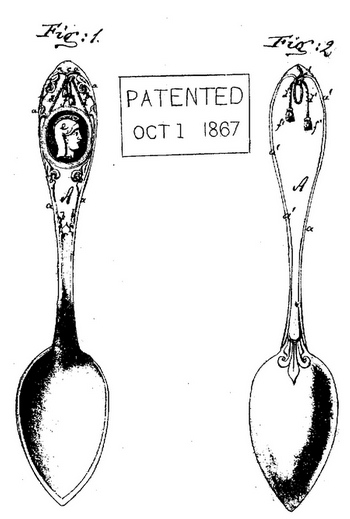
- Patent: 2,794, on 1 Oct 1867. LUTHER BOARDMAN AND NORMAN S. BOARDMAN, OF EAST HADDAM, CONNECTICUT.
DESIGN FOR A SPOON-HANDLE,
TO ALL WHOM IT MAY CONCERN:
Be it known that we, Luther Boardman and Norman S. Boardman, of East Haddam, in the county of Middlesex, and State of Connecticut, have invented a new and improved Design for Spoon and Fork-Handles; and we do hereby declare that the following is a full, clear, and exact description thereof, which will enable others skilled in the art to understand the same, reference being had to the accompanying drawings, forming part of this specification.
Figure 1 represents a front view of a spoon-handle ornamented with our new design.
Figure 2 is a back view of the same.
Similar letters of reference indicate corresponding parts.
This design relates to a new style of ornamenting for the upper part of a fork or spoon-handle, whereby the appearance of the same is greatly improved.
The invention consists in suspending a medallion or other suitable ornament, by means of tassclled cords, from a hook which is formed in arabesques arranged around the edge of the handle. On the back of the handle the tasselled cord is also arranged, being suspended from a hook formed by beaded mouldings arranged around the rim of the handle.
A represents the spoon or fork-handle. Around its edge is arranged, in front, a beaded moulding, a, ornamented by foliage or arabesques 6, as shown in fig. 1. The beaded moulding does not extend around the upper edge of the handle, but near the same it is turned in from each side, and the two mouldings from the two edges of the spoon are joined, forming a hook, e, at their junction, as shown in fig. 1. From this hook is suspended, by means of a cord or cords, d, an ornamental medallion, e, or any other suitable design, as, for example, a fruit-basket. The ends of the cord are provided with tassels f, as shown. On the back of the handle A a hook, c', is formed, by beaded mouldings a', in a similar manner as on the front of the handle. The beaded mouldings are plain on the back, that is, without arabesques. A tasselled cord, d', is suspended from the hook c', as is clearly shown in fig. 2.
We claim as new, and desire to secure by Letters Patent—
The design for a spoon-handle, substantially as shown and described.
LUTHER BOARDMAN,
NORMAN S. BOARDMAN.
Witnesses:
Geo. S. Richmond,
Jeremiah Ackley.
- He appeared on the census in 1870 in East Haddam CT. Listed as a nickel silver and britannia spoon manufacturer.
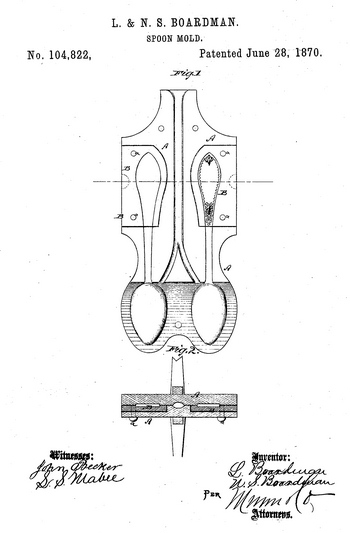
- Patent: 104,822, on 28 Jun 1870. LUTHER BOARDMAN AND NORMAN S. BOARDMAN, OF EAST HADDAM, CONNECTICUT.
Letters Patent No. 104,822, dated June 28, 1870.
IMPROVEMENT IN SPOON-MOLDS.
The Schedule referred to in these Letters Patent and making part of the same
To all whom it may concern: Be it known that we, LUTHER BOARDMAN and NORMAN S. BOARDMAN, of East Haddam, in the county of Middlesex and State of Connecticut, have invented a new and improved Mold for Casting Spoons; and we do hereby declare that the following is a full, clear, and exact description thereof, which will enable others skilled in the art to make and use the same, reference being had to the accompanying drawing forming part of this specification, in which—
Figure 1 represents a face view of our improved mold for casting spoons.
Figure 2 is a transverse section of the same.
Similar letters of reference indicate corresponding parts.
This invention has for its object to reduce the expense of molds for easting spoons of britannia or other metal.
Such molds had heretofore to be specially prepared for every new design or variation of design of the spoon-handle, and their expense was consequently considerable. As the chief variation in the design is mostly in the handle, and frequently only on the face of the handle, we have found it necessary to renew the entire mold whenever a small change took place.
Our invention consists, therefore, in applying to the mold A a removable section, B, which constitutes that part of the mold where the design is most frequently changed. The section B is made of steel, or other suitable material, and is inserted in a recess provided for it in the main mold, so that it will fit flush into and form part of the said mold.
The groove or projections pertaining to the design are continued in the plate B, in the same manner as though the same was made in one piece with the mold. Whenever that part of the design which is engraved on the plate B is changed another such plate is placed into the mold, without requiring any change of the mold itself.
Screws, a a, or other devices, serve to retain the plates B in the molds, and permit their ready removal and replacement.
The invention is equally applicable to single and double molds, and to either or both cheeks or parts of each.
Having thus described our invention,
We claim as new and desire to secure by Letters Patent—
The spoon-mold A, provided with the removable section B, substantially as and for the purpose herein shown and described.
Luther Boardman
Norman S. Boardman
Witnesses:
J. Attwood
J. Ackley
- He appeared on the census in 1880 in East Haddam CT. Listed as a silver manufacturer.
Luther married Lydia Ann Frary, daughter of James Frary and Anne Taylor, on 18 Oct 1838 in Meriden CT. (Lydia Ann Frary was born on 15 Mar 1815 in Meriden CT and died on 27 Jun 1909.)
|