Orson William Stow
- Born: 30 May 1820, Rocky Hill CT
- Marriage (1): Sarah Walkley on 13 Jun 1840 in Southington CT
- Died: 11 Nov 1883, Southington CT
General notes:
Silverplate manfacturer
Events in his life were:
- He appeared on the census in 1850 in Southington CT. Listed as a machinist.
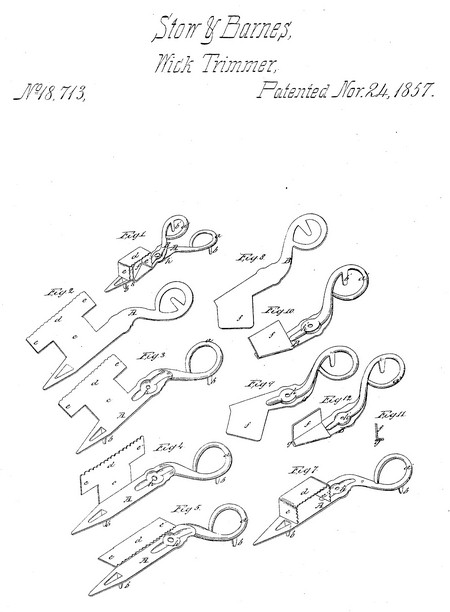
- Patent: 18,713, on 24 Nov 1857. O. W. STOW AND AUGUSTUS BARNES, OF SOUTHINGTON, CONNECTICUT.
IMPROVEMENT IN CANDLE-SNUFFERS.
Specification forming part of Letters Patent No. 18,713, dated November 24, 1857.
To all whom it may concern:
Be it known that we, O. W. STOW and AUGUSTUS BARNES, of Southington, Hartford county, and State of Connecticut, have invented a new and useful Improvement in Candle-Snuffers, constituting an improved article of manufacture; and we do here by declare that the following is a full and exact description of the construction, operation, and advantages of our improvement, reference being had to the annexed drawings, forming a part of this specification, in which—
Figure 1 is a perspective view of our improved snuffers as they appear when completely finished, and Figs. 2, 3, 4, 5, and 7, views of the bowl portion at different stages of the process of manufacture; Figs. 8, 9,10, 11, and 12, views of the extinguisher portion during different stages of the process.
Similar letters of reference indicate the same parts in all the figures.
Our improvement consists in an improved article of manufacture, viz., candle-snuffers, much substantially as hereinafter described. The common snuffers are composed of six distinct pieces of inetal (irrespective of the spring and rivet) which are either cast or forged, according to the inetal of whicli they are composed. If of steel, they are forged; if of iron, they are cast. The former are considered the best kind and cost the most. The latter are the cheapest and least durable.
The parts are, 1 the bottom part, 2 the bowl, 3 the cutter part, and 4, 5, and 6 three legs. All of these parts are made separate and involve in their combination no less than fifteen distinct operations, as follows: 1, 2. 3, 4, 5, and 6, casting or forging of the parts; 7, 8, and 9, drilling three holes for the legs; 11, 12, and 13, riveting the three legs: 14, fitting the bowl to its bottom with a file; 15, brazing the bowl to the bottom.
The subsequent operations of polishing and finishing need not be described.
The common snuffers made as above are heavy, clumsy, weak, and inconvenient. Owing to their weight they cannot be held over the flame of the candle with convenient steadiness and the result is that the candle is frequently extinguished in the act of snuffing the wick. Again, if dropped upon the floor they are very liable to break. Either the point snaps off or the legs, or the blades, or the bowl. This is owing to their weight; but their construction forbids any diminution thereof. It is a matter of great rarity to find in any household a single pair of snuffers, among those that are in constant use, that are not broken in some part.
Our improved snuffers are composed of two pieces only, each of which is cut from sheet metal by a single blow of a drop-press. Only nine operations are required to produce the complete article ready for polishing. The upper or bowl-wing part A is first cut out in blank, as shown in Fig. 2. It is then corrugated and the finger-rings a and legs & formed all by a second blow. The corrugations give the necessary stiffness to the sheet metal.
The plate is then put in a machine which bends up the bowl portions c d e, as shown, respectively, in Figs. 4, 5, and 7. The end e' of the bowl part is cut a little shorter than c, in order to permit the cutter part B to pass under the end e' when in operation. The legs 1) are then bent down, when the bowlwing is complete. By the aid of the machine before mentioned a boy bends six hundred of the bowl-wings per hour. The blank cutter-wing B is cut at one blow in the same manner as the bowl part A, (see Fig. 8,) and then corrugation finger-ring a' and the leg b' formed as in Fig. 9. It is then put into a machine and the projecting part f is bent thereby, as in Figs. 9 and 10, so as to form a suitable cutting-edge for the purpose of clipping the candle-wick. A boy aided by the machine bends nine hundred cutter-wings per hour.
Fig. 11 is an end section of the cutter-wing B. It will be observed that the cutting-edge g projects a short distance beyond the perpendicular portion f. This formation insures a better and more certain cut of the wick than the ordinary snuffers.
Fig. 12 shows the cutter-wing B complete ready for union to wing A.
The peculiar formation given to wing B, as shown in Fig. 12, adds strength and durability to the wing, the cutting portion being stiff and a cutting-edge much superior to that of the common snuffers being obtained.
When the two parts A B are put together, a hollow cavity h h' is left in the middle which receives the usual coil-spring. A rivet. passes through the center of the cavity and unites the two wings. The snuffers are then complete ready for use. If a high finish is wanted, they may be subjected to the galvanic battery and plated with gold or silver. Thus finished they present a very rich and beautiful appearance.
The snuffers commonly used in this country are imported from Europe, the labor attending their manufacture being so great as to prevent their production in this country.
The labor of making our improved snuffers is only about one-fifth that required to produce the ordinary article. We are therefore enabled to sell the improvement at prices much below the cost of the common article.
The labor of brazing on the bowl part of the ordinary snuffers is greater than that required to make a complete pair of our snuffers. If the die which cuts our blanks be suitably prepared, any desired ornamental configuration may be imparted to the snuffers without additional expense.
Our snuffers may be made of any kind of pliable rolled metal. The common sheet-tin forms a good substance for their manufacture. We make our cheapest kinds from this stock, and the snuffers when finished are far more strong and durable than the common cast-iron snuffers. For the finer kinds of our article we use rolled brass.
The common snuffers are liable to break by falling to the floor from the height of an ordinary table. The superior strength of our snuffers may be readily tested by throwing up a pair of each kind into the air and allowing them to fall. The joint, leg, or other part of the old kind will break; but the most that can happen to our snuffers is a slight bending of some portion which is readily restored.
The extreme lightness of our snuffers renders them very convenient in use, for the candle can be accurately clipped, as the weight is not sufficient to pull down the ends of the fingers unduly and thus produce an unsteady movement of the hand.
Having thus described our invention, we claim and desire to secure by Letters Patent as an improved article of manufacture—
The snuffers A B, struck out of sheet metal, the legs formed with and constituting a portion of the wing-blanks, and the cutter-wing B, bent, as set forth, so as to form a good cutting-edge, all as described.
O. W. Stow
Augustus Barnes
Witnesses:
J. S. Barnes
Laura Barnes
- He appeared on the census in 1870 in Southington CT. Listed as the secretary/treasurer of a hardware company
- He appeared on the census in 1880 in Southington CT. Listed as a manufacturer.
Orson married Sarah Walkley on 13 Jun 1840 in Southington CT. (Sarah Walkley was born on 3 Jan 1821 in Southington CT.)
|