John Simmons Palmer
- Born: 22 Mar 1824, Newport RI
- Marriage (1): Frances M. Prentice on 24 Aug 1848 in Providence RI
- Died: 8 Jul 1908, Providence RI
General notes:
Jeweler
Events in his life were:
- Apprenticed: G. & S. Owens, in Sep 1840, in Providence RI.
- Partnership: Christian Stave, in 1843, in Providence RI. As PALMER & STAVE.
- He appeared on the census in 1850 in Providence RI. Listed as a jeweler.
- Partnership: Charles Smith Capron, in 1852-1891, in Providence RI. As PALMER & CAPRON. After Capron's retirement, the firm name was maintained until Palmer's death.
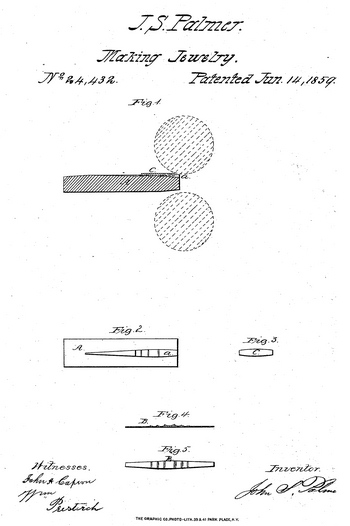
- Patent: 24,432, on 14 Jun 1859. JOHN S. PALMER, OF PROVIDENCE, RHODE ISLAND, ASSIGNOR TO HIMSELF AND CHAS S. CAPRON OF SAME PLACE
ROLLING METAL FOR JEWELRY.
Specification of Letters Patent No. 24,432, dated June 14, 1859.
To all whom it may concern:
Be it known that I, JOHN S. PALMER, of Providence, in the county of Providence and State of Rhode Island, have invented a new and useful Method of Roiling Out Jewelry; and I do hereby declare that the following is a full, clear, and exact description of the same, reference being had to the accompanying drawings, forming part of this specification, in which—
Figure 1 represents a longitudinal central section of the die which I use in rolling out articles of jewelry. Fig. 2 is a plan or top view of ditto. Fig. 3 is a plan of the stock from which a certain article of jewelry is to be manufactured. Fig. 4 is a longitudinal vertical section of the article after having been rolled out and Fig. 5 is a plan or top view of ditto.
Similar letters of reference in the several views indicate corresponding parts of my invention.
In rolling out articles of jewelry or in fact any other article the usual method is to pass the stock through between pressing rollers, or to place the stock on a die and pass pressing rollers over it, commencing at one end of the stock and rolling through to the other end or as far as the nature of the work requires. By doing this the stock is stretched from one end toward the other, and when it becomes necessary to raise certain portions of the work, such as the scale of a finger ring, the rolling in this manner was found to be insufficient, as by a continuous rolling from end to end the stock is carried forward and there is not sufficient remaining to fill the end of the scale. In order to produce such articles as the scale of a finger ring for instance, it has been necessary, to attach to the original plate an additional thickness of metal by soldering or by some other means, causing much more labor than would be required if the whole could be made out of one piece.
To accomplish this, namely to produce articles of unequal thickness and with the thickest part in the center by rolling, is the object of my invention, which consists, in arranging a tapering die with a suitable groove, in such a manner, that when the stock is placed on the same and it together with the die is passed through between a pair of pressing rollers, these rollers take first on the middle of the stock, whereby the same is pressed down into the deepest part, in the middle of the groove and it is drawn out toward one end and formed as directed by the groove, and by turning it the other end is rolled out in the same manner, so that I am enabled to raise the scale of a finger ring or any other similar article with perfectly sharp corners and of any depth. To enable those skilled in the art to fully understand, use, and construct my invention, I will proceed to describe it. A is a die made of steel and sufficiently thick to resist a very strong pressure. The upper face of this die is provided with a groove a the bottom of which is shaped according to the article of jewelry to be rolled by it. The groove represented in the die A in Figs. 1 and 2 is made for a ring, and it is intended to roll out a plate B as represented in Figs. 4 and 5. By referring to Fig. 4 it will be seen that the plate has its thickest part in the middle, from whence it is gradually thinning down toward both ends and several moldings on each side are intended to give to the ring a more ornamental appearance. The bottom of the groove a shows the same moldings reversed, those parts which are to be the highest on the plate B, being the lowest in the groove as will be easily understood from Fig. 1, and as the plate B becomes gradually thinner and narrower toward both ends, so the inner end of the groove a has to be made running out gradually to the surface of the die as represented in Fig. 1 and becomes narrower from the middle toward its end as clearly represented in Fig. 2. The front end of the die A is chamfered off at its under side and the groove a is made deep enough so that the pressing-rollers don't begin to act on the stock C, which is placed on the die as represented in Fig. 1 in red lines, before the die has passed far enough between the same so as to form the middle part of the plate B first. The stock is of uniform thickness throughout and thick enough to form the thickest part of the article to be rolled, and it is of such a shape that it just fits into the widest part of the groove a.
The operation is as follows: The stock is placed on the die as represented in Fig. 1 and the die is passed through between the pressing rollers, and the stock is not taken any thicker, than necessary to fill up the deepest part of the groove a, and as the die is so shaped, that the pressing rollers take first right above the deepest part of the groove a, the stick is pressed down into this part and its end is gradually thinned out toward the end of the groove, following the latter, and filling up all the inequalities on its ground. The stock is now taken out and its other end, which preserved its original thickness during the first part of the operation is placed on the die and passed through between the pressing rollers and it is drawn out in the same manner, following the groove a from the middle or deepest part of the same to its end. It is obvious that, with a die of uniform thickness from end to end, this object cannot be obtained, without the use of a male and female die or some part to take the place of the male die, whereas by making the die tapering on its front end I am enabled to raise the scale for a finger ring or other parts of similar articles with perfectly sharp corners and of any depth, nothing else being required but a female die and a pair of smooth pressing rollers.
Having thus fully described my invention what I claim as new and desire to secure by Letters Patent, is,
The employment of a tapering die A, in combination with the pressing rollers, substantially as and for the purpose specified.
John S. Palmer
Witnesses:
John A. Capron
Wm. Prestwick
- He appeared on the census in 1860 in Providence RI. Listed as a master jeweler.
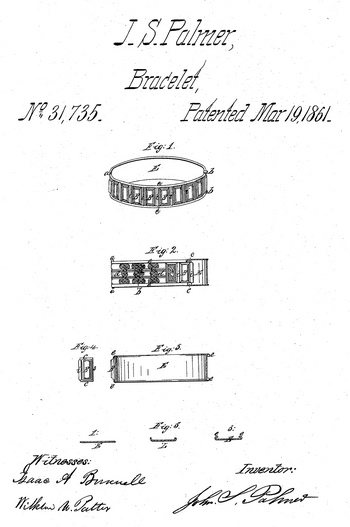
- Patent: 31,735, on 19 Mar 1861. JOHN S. PALMER, OF PROVIDENCE, RHODE ISLAND.
CONSTRUCTING BRACELETS, &c.
Specification forming part of Letters Patent No. 31,735, dated March 19, 1861; Reissued September 9, 1873, No. 5,571.
To all whom it may concern:
Be it known that I, JOHN S. PALMER, of Providence, in the county of Providence and State of Rhode Island, have invented a new and useful improvement in constructing bracelets, which is also applicable in constructing finger-rings, ear-hoops, and some other articles of jewelry; and I do hereby declare that the following is a full, clear, and exact description thereof, reference being had to the annexed drawings, and to the letters of reference marked thereon, in which—
Figure 1, is a perspective view of my improved bracelet. Fig. 2, is a front view and section of the same. Figs. 3, 4, 5, &c. are details which are referred to in the course of the description.
Similar letters of reference denote like parts in all the figures.
It has formerly been the practice to form the front or ornamental plate of such bracelets in one piece, with the edges turned at right angles therefrom, after which the superfluous stock is trimmed off, and the said edge soldered to a flat plate or lining, and the superfluous stock trimmed therefrom. The die which stamps or forms the ornamental plate is expensive and if a portion of the design is defaced by accident or otherwise, the whole die is rendered worthless. Again as each die produces but one design, a number of such dies are necessary to produce a variety of patterns or styles. In addition to this the trimming off the edge of the lining, leaves the baser metal exposed, (plated stock being generally used,) which coming in contact with the wrist of the wearer, forms an oxid which penetrates the soldered joint and separates the lining from the front.
My invention consists in turning over the edges of the foundation plate, to form an overlying lip, (or slide,) upon each edge of the outside of the bracelet, which forms a smooth round edge, and serves to support and retain certain ornamental work, composed of a number of metal plates, of designs in bas-relief, or chased work, or suitable plates containing hair work, precious stones, or miniatures, whereby different combinations of ornamental work may be produced upon one foundation plate, and thus, a great variety of styles, at much less expense than by the ordinary process of manufacture.
To enable others skilled in the art to make and use of my invention I will proceed to describe the construction and operation; A strip of metal of the width shown in Fig. 5, No. 1, is passed through a set of rolls, which turn the edges as shown in No. 2, and again through another set of rolls. which turn the edges as shown in No. 3,—the form of the rolls, and the mode of operation being sufficiently familiar to workers in sheet metal to require no description here. The turning or rolling the edges of similar rings of sheet metal, is also generally practiced to stiffen such rings, and for that purpose is well known, and I do not pretend is my invention.
The above stock is formed into a ring or oval, composed of two pieces, which are united at a, Fig. 1, in a hinge joint and at 5, by a catch or spring fastening.
Fig. 4, represents an ornamental'plate of die work in bas-relief, having projecting lips (or edges) c, c, at each end, and a ridge or bead i, which overlaps the opposite thin edge s, upon the adjoining plate, and hides the intervening space, as shown in Fig. 2. d, Fig. 2, represents a metal plate having openings therein, beneath which (plate) is placed braided hair-work l, which is visible through the said opening, and which by contrast with the polished metal plate produces a highly ornamental effect. These ornaments are slid beneath the lips e, e, of the foundation plate, in their proper order and position, the lips e, e, overlapping the lips c, c, of the plates B, B, and the beads i, overlying the thin edges s, of the adjoining plate. (Figs. 2 and 3.) The plate inserted next to the joints a, and 5, of the bracelet, Figs. 1, and 2, is secured in its place, to the foundation plate by a rivet passing through both, and thus the several ornaments are permanently secured therein. Should the bracelet be bent or broken, it will only be necessary to remove the rivets, when the ornaments may be readily removed, and the injured parts repaired, or new parts substituted for those which are broken or defaced.
It will be observed that a multiplicity of designs in bas-relief or mountings of precious stones, shell, and hair work, etc., may be inserted and combined upon one bracelet, and every different combination produces a different style or pattern, and in such a manner that no soldering is required. The dies which stamp the ornamental plates are inexpensive compared with those for stamping an entire front or outer surface, and if one is injured, another of a like, or of a different design may be made to take its place at a trifling expense.
In the construction of finger-rings, ear hoops, and other articles upon this principle, it will only be necessary to vary the size and form of the foundation plate and ornaments, to combine a variety of designs and thus produce numerous styles of such articles. I do not claim turning over the edge of a ring of sheet metal by means of rolls, for the purpose of forming a rounded edge, or for stiffening such ring, as this is well known and not my invention.
I claim—
The combination of the lips e, e, of the foundation plate with the ornamental metal plates, or their equivalent, constructed in the manner substantially as described, for the purpose herein specified.
John S. Palmer.
Witnesses To Signature:
Isaac A. Brownell,
Francis Colwell. Jr.
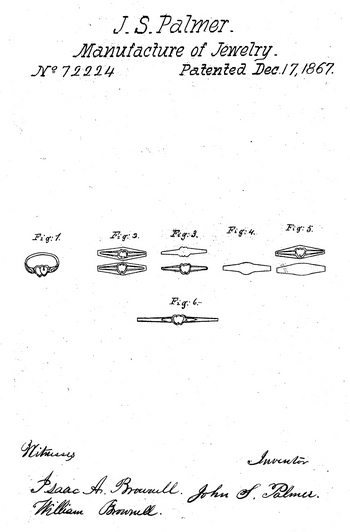
- Patent: 72,224, on 17 Dec 1867. JOHN S. PALMER, OF PROVIDENCE, RHODE ISLAND.
Letters Patent No. 72,224, dated December 17, 1867; antedated December 11, 1867.
IMPROVEMENT IN THE MANUFACTURE OF JEWELRY.
To All Whom It May Concern:
Be it known that I, JOHN S. PALMER, of the city and county of Providence, and State of Rhode Island, have invented certain new and useful Improvements in Making Jewelry; and I do hereby declare that the following is a full and exact description of the same, reference being had to the accompanying drawings, making part of this specification, in which—
Figure 1 is a perspective view of a finger-ring made in accordance with my said improvement.
Figure 2 is a plan of opposite sides of the struck-up shell used in making such ring.
Figure 3 is a plan of opposite sides of the alloy-filling used in making such ring.
Figure 4 is the lining-plate employed in the formation of said ring.
Figure 5 is a plan of opposite sides of the said shell, filling, and lining, united in a blank.
Figure 6 represents the form into which the blank (formed by uniting the said parts) is next wrought, by rolling, to give it the requisite shape to be converted into a ring, by bending and soldering the extreme ends together.
The usual mode of making shell jewelry is to raise the shell-piece from thin sheet stock, with all the fine figures and ornamentation in perfect form, by means of a suitable die and former beneath a drop-hammer, and afterwards filling the shell with chips or grains of solder and then applying the lining-piece and uniting the two pieces together by the flame of a blow-pipe or other means of melting the solder within the shell. By this method, however, the stock was required to be of such quality, thickness, and the shape and ornamentation of the shell were required to be of such a character as would resist the degree of heat, and not be melted or injured by the melting of the solder within it.
By the method which I have invented, I am enabled to work stock which is very much thinner than that heretofore employed, and without being limited or restricted in the quality, or shape, or ornamentation, as heretofore; and my invention, to this end, consists in striking up or raising the shell of a mere form or outline of the shape into which it is finally to be wrought, and in raising a shape or outline piece of solder or filling, which will fit into the said shell, and then applying the lining-piece, and melting the whole together, and after clipping the piece thus produced to remove the superfluous stock, by rolling or otherwise, shaping and ornamenting the piece in the form and manner desired to produce the complete and finished design.
In the drawings, fig. 2 is the shell as it is raised in the die, .it being, as will be seen by comparison with fig. 6, merely the general outline of the form required, and fig. 3 is the shape of solder or filling which is produced by punching from the sheet, and afterwards raising in a die beneath a drop. This piece is intended to fit into the shell quite nicely, but it is essential that it should fit completely and exactly in the bottom of the shell, and fit rather loosely at the top thereof, so that when the solder melts it will be sure to fill the deeper portions of the shell first, and by that means prevent the formation of air-bubbles on the surface of the shell by confining air between the shell and the filling. The sheet or lining-plate, fig. 4, is then placed over the filling-piece, and the whole subjected to a heat that will melt the filling and unite the three pieces into a solid mass, as shown in fig. 5. This piece is then clipped in the usual way to remove the thin fin of metal surrounding the shell, and the shell is then placed in a die having the form of the scale, (of the two heats,) and one of the sides, as shown in fig. 6, and this die, with the shell in it, is passed between a pair of rolls, after the manner set forth in Letters Patent, No. 24,432, granted to me, June 14,1859, and the shell-piece rolled into perfect form, with the required ornamental figures, the said piece being delivered in the form shown in fig. 6. This piece is then bent into its circular shape, and the extreme ends soldered together, and after being polished the ring is completed.
This method of first producing the general outline of a piece of jewelry, and after filling to roll or otherwise cement it into its perfect ornamental shape, enables me to use a requisite thickness of shell to withstand the heat required to melt the filling, and afterwards to reduce and draw out the stock to a degree of thinness to which it could not possibly be reduced or worked by any process hitherto employed in making this class of work, and although I have only described above the process of making finger-rings by this method, it will readily bo understood that the said method is also applicable to the making of other articles of jewelry in which the metal shape produced by uniting an external shell and filling is capable of being reduced by the process of rolling mentioned, or an equivalent operation, to the complete and perfect form, with its required ornamentation.
What I claim, and desire to secure by Letters Patent, is —
1. Forming the raised metal shell merely of the general outline of the shape in which it is finally to be produced, substantially as and for the purpose specified.
2. Forming the alloy filling of a shape to fit the interior of the said shell, in one piece or shape, substantially as and for the purpose specified.
3. Reducing the said outline shell and the filling, after the same have been united into one piece, as described, to its perfect finished shape, and ornamenting the same by rolling or other suitable means, substantially in the manner described.
In testimony whereof, I have hereunto set my hand, this nineteenth day of November, A. D. 1866.
John S. Palmer
Witnesses:
Isaac A. Brownell
William Brownell
- He appeared on the census in 1870 in Providence RI. Listed as a manufacturing jeweler.
- He appeared on the census in 1880 in Providence RI. Listed as a manufacturing jeweler.
John married Frances M. Prentice on 24 Aug 1848 in Providence RI. (Frances M. Prentice was born on 13 Mar 1828 and died on 7 Jul 1906.)
|